Pid Controller Is Used for Which Type of Compensation
Output P It D. PID Controller Output Math.
Pid Controller Theory Instrumentation Tools
Derivative controller DC 11 Role of a Proportional Controller PC.
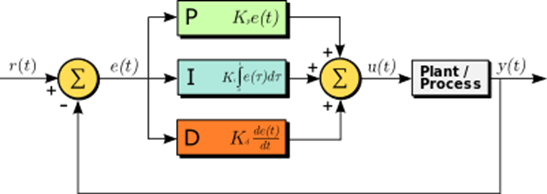
. Due to robust performance and functional simplicity these have been accepted by enormous industrial applications where a more precise control is the foremost requirement. PID temperature controllers work using a formula to calculate the difference between the desired temperature setpoint and current process temperature then predicts how much power to use in subsequent process cycles to ensure the process. Proportional controller PC 2.
This standard PID controller combines proportional control with integral and derivative control PID which helps the unit automatically compensate for changes in the system. They are also referred to by their reciprocals RESET and RATE respectively. However to have high performance a more sophisticated compensation network is required especially when MLCC Multi Layer Ceramic Capacitor capacitors are used.
These controllers are also referred through their reciprocals RATE RESET correspondingly. The process of stabilizing servo drives has been described as an equalization process or some times referred to as compensation of a servo system. A PID controller is actually a three part system.
Modern commercial servo drives use digital algorithms to implement PID type compensation. PID which stands for proportional integral derivative controllers use a control loop feedback mechanism to control process variables and are the most accurate and stable controller. PID Control Definition.
PID Control with Intelligent Compensation for Exoskeleton Robots explains how to use neural PD and PID controls to reduce integration gain and provides explicit conditions on how to select linear PID gains using proof of semi-global asymptotic stability and local asymptotic stability with a velocity observer. George Younkin PE MSEE. O P controller involves only a proportional gain or attenuation.
A PID controller is an instrument used in industrial control applications to regulate temperature flow pressure speed and other process variables. PID controllers are used for more precise and accurate control of various parameters. Shri Guru Gobind Singhji Institute of Engineering and Technology For the controller PPIPD PID the design is used for not only filtering but controlling is the main functionand repeatedly it.
MLCC capacitors are widely used at the output of low voltage DCDC converters because of their low. For the individual designer analog compensation techniques can be used to implement the required compensation as has been the case for. Err Sp PV.
The basic types of PID controller are parallel controller serial controller and mixed controller. In its simplest terms PID is a type of control used to stabilize servo drives. Integral derivative controller PID controller is a method of the control loop feedback.
PID is acronym for Proportional Plus Integral Plus Derivative ControllerIt is a control loop feedback mechanism controller widely used in industrial control systems due to their robust performance in a wide range of operating conditions simplicityIn This PID Controller Introduction I have Tried To Illustrate The PID Controller With SIMPLE Explanations BASIC. All together a PID control loop looks like this. The main function of the proportional compensator is to introduce a gain that is proportional to the error reading which is.
T Gain dB 0 20. PID controller is most commonly used algorithm for controller design and it is most widely used controller in industry. Improve the phase of the power stage.
These modifications integral derivative are expressed in time-based units. Optimize a particular control system. PID temperature control is a loop control feature found on most process controllers to improve the accuracy of the process.
This method is composing of three controllers 1. This kind of PID controller will merge proportional control through integral derivative control to automatically assist the unit to compensate modifications within the system. This is not recommended practice for individual designers unless they have the digital background necessary.
O Controller input is error reference output o Controller output is control signal. Derivative controllers differentiate error. Stabilized with a proportional-integral PI type of compensator.
PID can be implemented either in analog or digital and be used with hydraulic or electrical servo drives. Most often these are used for the regulation of temperature pressure speed flow and other process variables. Integral controller IC 3.
For this reason Type II compensators cannot be used for voltage-mode control in CCM where there is a large phase drop just after the resonant frequency. Depending on the gain setting of these three values will determine how much effect they will have on the output. U K p e.
The controllers used in industry are either PID controller or its improved version. Integral controllers integrate error. Proportional-Integral-Derivative PID control is the most common control algorithm used in industry and has been universally accepted in industrial control.
The PID controller output is calculated by simply adding the Proportional the Integral and the Derivative. Proportional controllers pure gain or attenuation. Type II compensators are usually reserved for current-mode control compensation or for converters that always operate in the DCM region.
P kP x Err. These conditions are applied in both task and joint spaces with PID. These adjustments integral and derivative are expressed in time-based units.
The popularity of PID controllers can be attributed partly to their robust performance in a wide range of operating conditions and partly to their functional simplicity which allows engineers to operate them in a.
What Is A Pid Controller Youtube
Pdf Pid Controller Without Noise Gayathri Addanki Academia Edu
Pid Controller Working Types Advantages Its Applications
What Is Pid Controller Learn Pid Controller Working Structure And Tuning Methods
Pid Controller In Control Systems
The Conventional Structure Of The Discrete Pid Controller Download Scientific Diagram
Pd Pi Pid Compensation Outline Pd Control Remarks
What Is Pid Controller Working Advantages Disadvantages Applications
Ideal Pid Controller Using Active Circuit Realization Youspice
What Is A Pid Controller Their Types And How Does It Work
Standard Pid Controller Structure Download Scientific Diagram
What Is Pid Controller Learn Pid Controller Working Structure And Tuning Methods
Structure Of Conventional Pid Controller Download Scientific Diagram
Pid Controller A Proportional Integral Derivative Controller Pid
Pid Controllers In Control Systems Electrical4u
Pid Controller Tuning Using Bacterial Quorum Sensing Qs
Multicopter Pid Tuning Guide Advanced Detailed Px4 User Guide
What Is Pid Controller And How It Works Electrical Industrial Automation Plc Programming Scada Pid Control System
Comments
Post a Comment